Request a quote
Get in touch
About
T-7/4S – BI-DENSITY POLYURETHANE INJECTOR & TPM-30/60 – STATIONARY MOLD DOOR
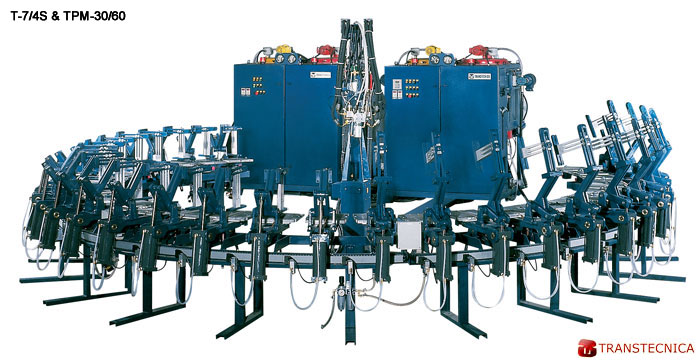
High-precision polyurethane dosing unit specially developed for the serial production of polyurethane soles that require the use of distinct raw material systems or for the production of bi-density soles. Precision dosing, ratio, and flow combined with commands through a programmable logic controller (PLC) allow the interchangeability of the injected components, enabling the production of diverse items in the same production line, such as midsoles for sneakers and soles for safety shoes. The system allows for sequential or alternate injection of a specific raw material system with color variation when connected to the color unit.
Features
Dosing Unit
- Mixing head for four components with pneumatic control
- Dynamic mixing grid driven by an electric motor and mixing chamber with cooling
- Measurement of each component through high-precision dosing pumps with independent drive for each
- Speed variation controlled through frequency converters activated by a keyboard with digital RPM display
- Constant recirculation of each component through pumps, mixing head, and material reservoir
- Jacketed and thermostated 300L component tanks with low-speed tank agitator
- Maximum/minimum level sensor with automatic replenishment through transfer pumps
- Controlled by a programmable logic controller (PLC) with a state-of-the-art microprocessor, condensing times (pre-injection, injection, cleaning cycle – pause/solvent/air), temperature control, providing statistical calculations of injections and washes, and functioning as a data concentrator
- Two-line liquid crystal display showing alphanumeric messages as variables for time, temperature, and the mold to be injected
- Synoptic panel with activation keyboard, digital indication of material line pressures, visual indication of electro/mechanical components in use
- Pressure indicator with safety contact to monitor injection and recirculation of each component line
- Control panel on the head with only one injection button to activate the injection into the pre-selected mold (system/color/time)
- Machine/mold gate interconnection and absolute encoder with automatic reading of a specific mold gate position, quantity of molds, type of raw material, color, injection time, mold closing and opening time
- Central tower with a rotating system and arm with a pneumatic system to control the vertical movement of the head
- Emergency cleaning auxiliary system
Mold Holder
- Modular mold holder with 6 stations for 6 feet/6 pairs (double matrix)
- Adjustable height for quick adaptation to the mold
- Quick mold change system (optional)
- Heating plate for each station
- Temperature control, mold opening, and closing through the controller
- Basic versions with 24, 30, 36, or 42 stations (TPM-24/48; TPM-30/60; TPM-36/72; TPM-42/84)
- Optional version with up to 60 stations (TPM-60/120)
- Injection system from the internal or external side of the mold holder as required
Necessary Services
Dosing Unit
- Electrical power: 220V or 380V/Three-phase/60 Hz
- Electrical Power: 36 kW (18 kW per unit)
- Air: 6 cfm at 120 psi
- Water: Industrial
Mold Holder (per station)
- Electrical power: 220V or 380V/Three-phase/60 Hz
- Electrical Power: 500W
- Air: 1.11 cfm at 120 psi per cycle
Dúvidas? Confira as perguntas frequentes
We embrace holistic development and support for employees with the aim of being a first-choice employer within our sectors. Through a unique combination of engineering, construction and design disciplines and expertise.
We embrace holistic development and support for employees with the aim of being a first-choice employer within our sectors. Through a unique combination of engineering, construction and design disciplines and expertise.
We embrace holistic development and support for employees with the aim of being a first-choice employer within our sectors. Through a unique combination of engineering, construction and design disciplines and expertise.